PROJECT DETAILS
Project Name: The RH Johnson Company, Blasting Parking Garage
Project Industry: Industrial Coating
Client: The RH Johnson Company
Size: 8,000 Sq Ft
Media Used: Black Beauty Coal Slag, Master Seal Coating, Pressure Washing, Waterproofing Membrane
Location: Kansas City, Missouri
REPAIR OR REPLACE? How many times have you asked yourself this question? Rather it is your coffee maker, refrigerator, vehicle, or house; anytime something isn’t functioning or looking 100% you have a choice to make.
To help make the decision, do you follow some simple calculation-based methods, like the 50 Percent Rule? This rule states if repairs exceed 50% of the total cost of replacement, then replace it. Other advice says when the cost of repair is less than the value, you should repair it, but when the cost of repair is higher than the value of the asset, you should replace it.
You could spend hours comparing quotes and costs to find an answer because let’s face it, no one wants to feel like they are just throwing money away.
When doing their own comparison on their multi-level parking garage, our client decided that a repair was the way to go. Over time, the concrete has been breaking down and the paint is failing which has resulted in rust and corrosion. This is threatening the stability of the structure and therefore causing damage to cars parked on the lower levels from falling debris. As you can imagine, the cost of rebuilding a parking structure is pretty high. For a fraction of the cost, Blast It Clean could extend the structure's life by at least another 10 years.
This project was a complete restoration, so there are multiple surfaces that needed our attention. We broke it down into three phases starting with the decking on the top level accompanied by the vertical concrete walls on the lower level. Next up were the steel decking, joists, columns, and horizontal concrete surfaces on the lower level. Finally, we finished up with steel rails surrounding the parking garage and balcony rails.
THE REMOVAL PROCESS
Blast It Clean kicked off the removal of phase one by Hydro Blasting to remove the current waterproof membrane in all areas. In addition to the parking structure decking, we used hydro blasting to remove existing paint from the concrete walls on both levels. Hydro blasting uses special water pumps to amplify pressure without any abrasive. It is powerful enough to completely remove the coating without causing further damage to the concrete surface below.
The main culprit causing damage to the structure is water. So, it was very important that we properly waterproof the decking on the top layer. This should prevent water from seeping down onto the metal structure below it causing rust and corrosion.
Removing the coating revealed all the cracks and joints in the concrete needing repair. Using Master Seal NP 1, all joints were caulked, priming first where necessary on larger gaps. Sealants are the first line of defense so it’s important we use a proven product with high-performance qualities. Master Seal NP 1 is an elastomeric polyurethane sealant that adheres to concrete and masonry without the need for a primer. Along with providing a weather-tight seal, it has superior flexibility ensuring a long-lasting seal on moving joints.
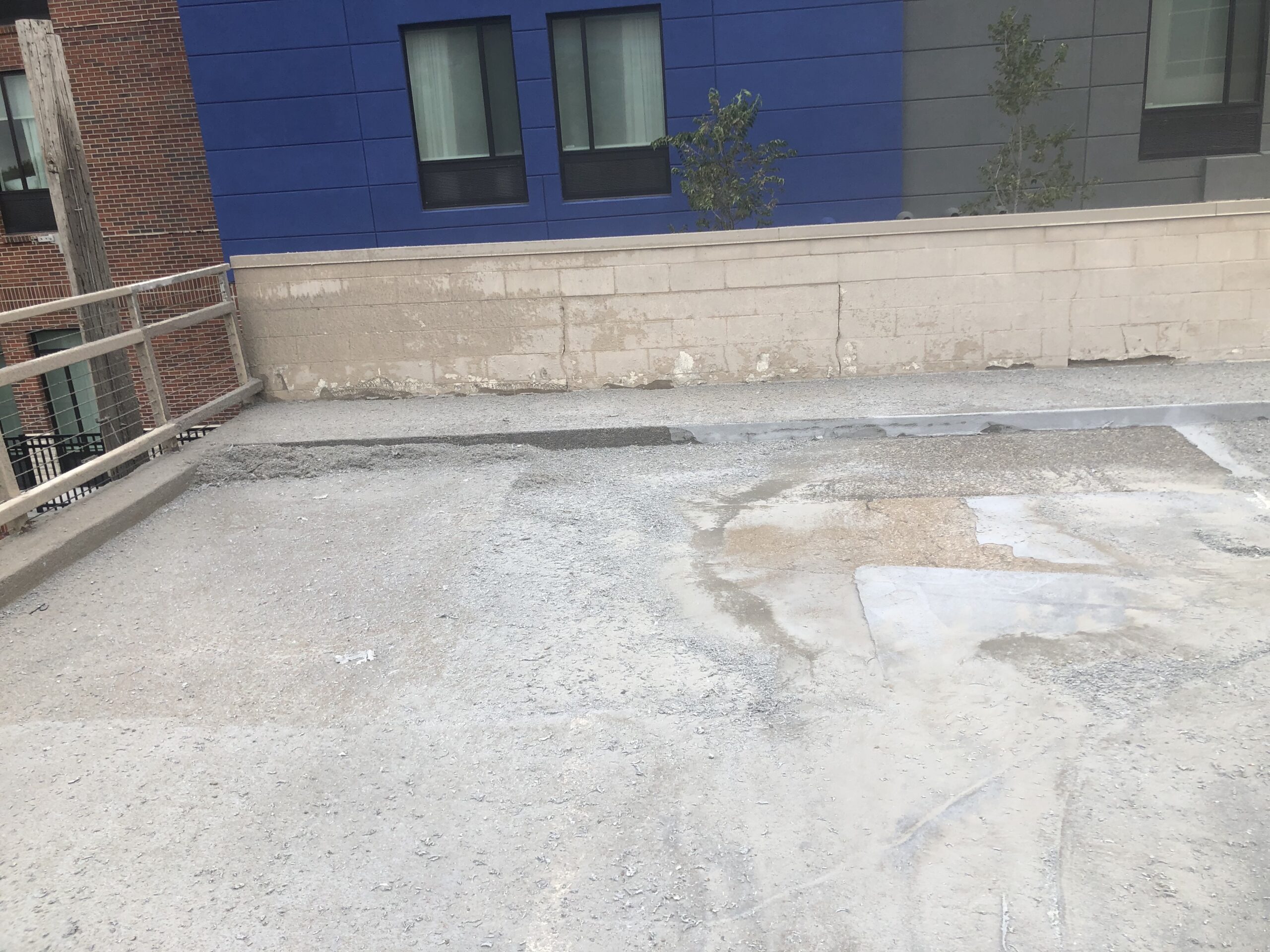

With removal and repair complete, we were able to apply a heavy-duty traffic-grade waterproofing membrane system from Master Seal. The traffic system uses multiple layers of moisture-curing polyurethane to create a tough barrier preventing water from infiltrating the structure. First is the base coat, Master Seal 200. This product is unique because of its strong adhesion qualities. Next, we applied an intermediate coat of Master Seal 225. This was backrolled to level then an aggregate was added. The aggregate helped to enhance the coating system qualifying it as a heavy-duty waterproof membrane. Finally, we applied the topcoat. Again, using Master Seal 225 we back-rolled followed by an aggregate. The aggregate used in the topcoat is spread at a lower rate than the intermediate coat. One final back roll completes the seal. In addition to the waterproofing, Master Seal TC 225 also provides a UV-resistant finish.
To achieve the goal of providing the optimal waterproof membrane, the coating was applied six inches up on all vertical surfaces it came in contact with. This assured a consistent barrier so there would be nowhere for the water to creep in.
The remainder of the vertical concrete surfaces were coated with Master Seal 581 after the patch and joint work were complete. MasterSeal 581 is a low-maintenance and highly durable waterproof barrier. It is a portland cement-based coating that is waterproof but is also breathable. Therefore, any interior moisture can escape without damage to the coating.
Establishing this waterproof membrane was the first step to preserving the structure and assuring a successful restoration.
To get started on solutions for your restoration project, give us a call at (877) 379-4233, or fill out an inquiry form on our website HERE.