VAPOR CLEANING WITH BLAST IT CLEAN
There are a couple of different techniques for introducing water into the blasting process. The first uses a special nozzle to spray water with the abrasive as it is propelled towards the surface. This dampens the impact of the abrasive and the dust that would be created.
The two widely used nozzles for this specific application are a halo nozzle or a water injection nozzle. A halo nozzle creates a ring around the abrasive blast shielding release of dust after impact. A water-Injection nozzle forcefully inserts jets of water into the abrasive as it exits the blasting nozzle. Using an attached nozzle to introduce the water to pressurized abrasive as it leaves the blasting nozzle slows it down thereby reducing potency. Both of these methods use quite a bit of water but can typically be used with traditional sandblasting equipment.
The second technique combines the abrasive with water in a compression pot. When the concoction is drawn through a constricted section into the compressed airflow this is called slurry blasting. When the mixture is forced by controlled water pressure into the airflow it is called fluidized blasting. These methods use less water and abrasives than the aforementioned nozzle methods.
WHAT IS VAPOR BLASTING?
When you think of “sandblasting”, what comes to mind? Dust? Mess? Harsh? Ultimately a lot of labor hours are designated to clean up and would offset the benefit. If there was one thing that could change all that, would it alter the way you think about using it for your facilities' stripping and cleaning needs? The solution you may be looking for could be as simple as water!
Call it vapor blasting, wet blasting, or dustless blasting. They all refer to the same idea of incorporating water with the blasting abrasive and compressed air to remove paint, grease, dirt, and debris from surfaces like concrete, stone, and metal.
Dry sandblasting is known to be aggressive, cutting into the surface and removing the top layer creating a new surface profile. While this helps with the adhesion of the new coating, your surface may not be up for this kind of abuse. In vapor blasting, the water helps soften the blow, disbursing the impact of the media. This more gentle approach results in a finer finish. It also opens the door for special media sandblasting to be used on softer surfaces.
Vapor blasting made its first appearance due to concerns regarding occupational hazards in the workplace environment. Sandblasting was banned in Europe, which led to innovative ideas using wet blasting. The invention of the first mobile wet blaster came to fruition in the 60s. The design was created in tandem with the sandblasting tool to produce a similar outcome but without the environmental hazard.
ADVANTAGES OF VAPOR BLASTING
Did we mention it is dustless? This is a huge advantage in specific situations. Although it is not 100% effective at eliminating any dust, the use of water significantly reduces contaminants released into the air. With no menacing dust clouds, vapor blasting can be performed in areas where there is a risk of infecting others nearby. This also reduces the amount of PPE (personal protection equipment) needing to be worn by workers like respirators. Additionally, vapor blasting can be performed in tandem with other contractors on a project without risking contamination. Dustless blasting could mean less downtime or shorter shutdowns for your facility.
Cutting down on dust reduces the amount of time and additional material needed to set up containment. Eliminating the plastic rolls and tape used to limit the distribution of spent media is less waste at the end of a project. This, along with the decreased risk of polluting the air, makes vapor blasting environmentally friendly.
Blast It Clean also uses many environmentally friendly abrasives like coal slag, walnut shells, crushed glass, and corn cobs. With vapor blasting, we are cleaning and stripping without the use of chemicals. This means no toxic byproducts are released and no additional pollutants are added to the water supply. Reducing the use of chemicals and diligent clean-up of blasting residue helps regulate pollutants in the surface water.
Another factor making vapor blasting an environmentally-conscious option is less consumption of media. When the abrasive is combined with water as described in the slurry or fluidized methods, it creates more mass and uses fewer media.
Besides dampening the dust, the introduction of water in blasting reduces heat transfer from friction. This is especially important when working on material that is subject to warping. It also reduces the wear and tear on equipment.
COMMON VAPOR BLASTING USES BY INDUSTRY
SUSCEPTIBLE SURFACES & SOFT METALS
When the surface that needs to be cleaned or stripped is delicate or is unable to withstand heat, wet blasting is a great option. Thanks to the water acting as a cushion and disbursing the impact of the abrasive, surfaces that are traditionally cleaned with chemicals can benefit from this environmentally friendly option.
When using water in the sanding process of surface preparation there is a risk that you may expose metal surfaces to the potential for flash corrosion. To remedy this concern, it is best to protect the metal with a rust-inhibiting sealer or primer as soon as possible. There are even rust-inhibiting solutions that promise to provide this when combined with water in the final washdown of the sanding process.
INDUSTRIAL
Vapor blasting is effective at removing grease build-up so it is an obvious fit for the automotive industry. It is also a great option in the oil and natural gas industry. With no toxic and dangerous dust plume or static build-up, explosion or fire are not dangerous with vapor blasting.
On every project cutting power, dust containment, and ability to withstand heat are all considered when determining the best special media sandblasting technique to utilize. When you weigh in the efficiency and environmentally friendly benefits it’s hard to overlook vapor blasting (wet blasting) as an option for your stripping and cleaning demands.
HISTORIC RESTORATION
When working with abrasive cleaning on historic buildings, comes with a harsh price. You could potentially reduce the life of the building material, such as brick, using traditional sandblasting methods. The heat transfer could cause warping or damage to the historic features of metal trim. Chemical or physical treatments can destroy or diminish the detailing of a building and in turn, can increase the water permeability to the brick on a wall. So what can be done to clean delicate surfaces gently? Use water or vapor of course!
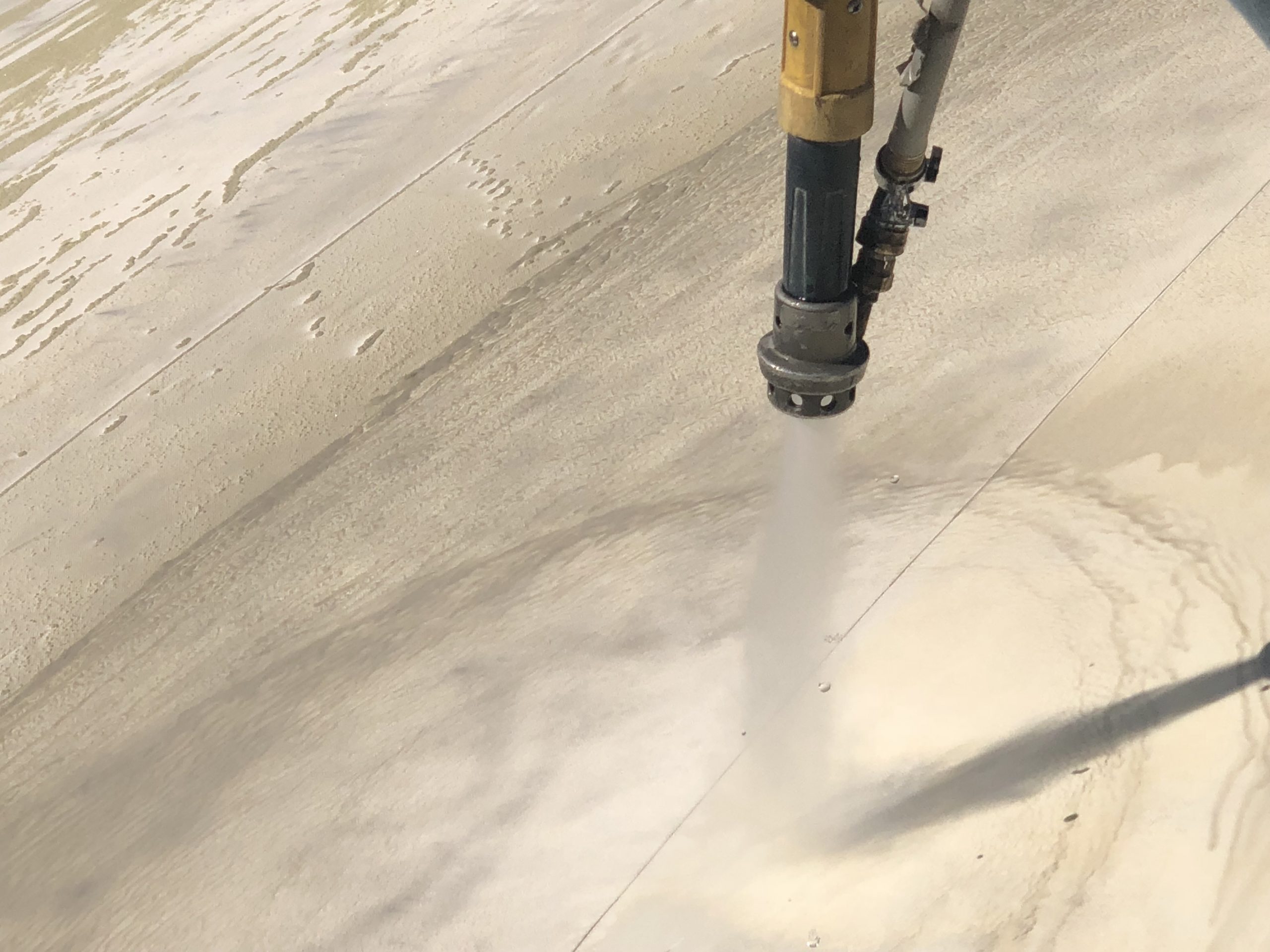
BLAST IT CLEAN - VAPOR BLASTING NATIONAL SERVICE PROVIDER
Does vapor blasting or any environmentally friendly abrasive blasting sound like something you need? We would be happy to help you with any upcoming projects you might have. If you think you have something that cannot be removed or cleaned, you might be shocked to know that chances are we can handle the job! Talk to our experts and we will find the best solution for your cleaning needs.