Employing Our Expertise in Food Safety
Imagine standing in a room of an industrial manufacturing facility that is bigger than a football field. In that massive space is large cooking equipment that emits hot, moist steam from the process of preparing food. If you look up, the steel structure of the building is exposed and has failing paint and visible rust. Do you see anything wrong with this visual?
Safety is a priority in every project we do so it’s easy to take all the details we focus on for granted. However, our extensive expertise working in the food manufacturing industry has prepared us for the described scene. The ceiling over this equipment is at risk of contaminating the food if it is not properly prepared and coated. That’s where Blast it Clean came in.
Due to continued growth, one of our favorite customers in the pet food industry needed to expand the production of their existing facility. They trusted us to devise and execute a plan to get the 67,000 sq. ft of their steel structure up to food safety standards.

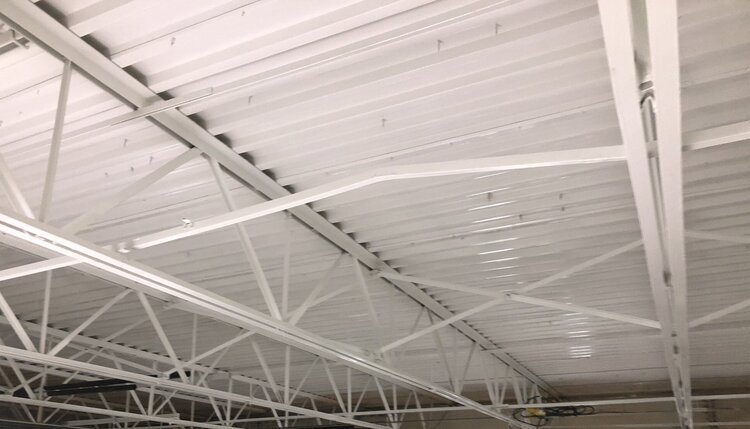
Since this was a restoration of an existing and operational facility, there was equipment that needed to be protected and shared airflow with current production. To minimize the potential for contamination, Blast It Clean divided the room into 3 sections to be completed over the course of 3 dedicated weekends. Starting Friday and finishing up Sunday evening, we had 10 members of our team alternating 12 hours shifts (5 on 5 off) during the 48 hours the facility was shut down.
During those 48 hours, Blast It Clean set up a full containment system with negative airflow. Specifically, a 6-mil poly to form a surrounding barrier on all areas needing protection from cross-contamination. This was to shield from over-spray and debris to avoid particles polluting the food processing equipment. The negative airflow system helped to trap VOCs and clean contaminants from the surrounding area to ensure the facility would be up and running for production immediately following our work.
With proper containment in place, we could get to work on the most essential stage of any corrosion protection system, surface preparation. If the surface is not properly prepared, the coating applied will likely fail to result in corrosion and thus voiding the protective coating altogether. To our customers, that means a waste of time and money as well as, potentially, food contamination.
First, we needed to remove the heavy rust to get the steel down to a paintable surface. Then an abrasive blast was required to remove all dirt, grime, grease, build-up, and leave a desirable surface for the coating to adhere. In another industry, we may have chosen a different abrasive to prepare the surface but since we were working in the food industry, we used Dry Ice to clean all areas. Dry Ice is approved by the FDA. In addition to its ability to clean and prepare the surface, dry ice sanitizes it as well. It also does not leave any residue behind. All of these factors were vital to the safety standards of the food manufacturing facility.
BLASTING FOR THE FOOD & BEVERAGE INDUSTRY
Atmospheric hazards are the primary cause of unfavorable outcomes due to working in confined spaces. Harmful gasses can be colorless and odorless and even if they are detectable there is no way to know the extent without instrument testing. Monitoring includes oxygen levels as well as the presence of flammable gases. This testing and evaluation must be complete before entry and is done continuously throughout the project.
Mechanical ventilation is the preferred method of correcting any atmospheric concerns. Blowing fresh air displaces the hazardous gas and lowers its concentration within the confined space. As an extra precaution, the hood each blaster is required to wear as part of their PPE (personal has fresh air being pumped into it.
All members of our team are trained and qualified to complete the necessary safety protocols. However, there is a difference between taking a training course and having the experience and a company culture that emphasizes safety. Working in confined spaces is something the team at Blast It Clean does nearly every week. Due to the nature of our work, the PPE is already a standard requirement so many times we are just adding air monitors and lighting to our equipment load. We are familiar with the risks and steps we can take to minimize them. It doesn’t matter if it is a one-time silo restoration or a weekly tank cleaning, confined space safety must be followed every time.
If you have a confined space that needs a team of professionals, call Blast It Clean for stripping, cleaning, and painting.