Focus on Preventative Maintenance in Your Food Manufacturing Facility
"Time is Money." This adage holds true across industries, and in manufacturing, it becomes even more significant. Manufacturing processes involve various timing factors, including lead time and cycle time, but one factor stands out as the most critical: downtime. Downtime refers to the period when production is halted, resulting in lost productivity and potential revenue. In today's competitive landscape, it's not enough to simply work faster to make the most of your time. To truly capitalize on this invaluable resource, a smart and strategic approach is necessary to minimize disruptions to production while maximizing the use of downtime.
This is where a well-executed routine maintenance plan comes into play. By implementing a proactive maintenance strategy, you can address potential issues before they escalate into major problems that result in prolonged downtime. Regularly monitoring equipment performance, conducting inspections, and performing preventive maintenance tasks can help identify and rectify minor concerns, ensuring that your machinery operates efficiently and reliably.
Prioritizing a routine maintenance plan brings a multitude of benefits. Firstly, it helps minimize unplanned breakdowns. By taking a proactive stance, you significantly reduce the chances of sudden equipment failures that can bring your production to a halt. This not only saves valuable time but also mitigates the need for emergency repairs, which tend to be costlier and more time-consuming.
Moreover, a well-planned maintenance plan contributes to regulatory compliance, especially in industries like food manufacturing. Adhering to health and safety regulations is crucial for maintaining the quality and integrity of your products. Routine maintenance tasks such as tank blasting, cleaning, and maintaining proper coatings ensure that your equipment meets regulatory standards, thus minimizing the risk of contamination or product spoilage.
HOW DOES A PREVENTATIVE MAINTENANCE PLAN HELP?
The idea is the same as getting your oil changed regularly. The hope is you can avoid being stranded on the side of the highway looking at an exuberant repair bill. Eliminating all unplanned breakdowns would be nice, but unrealistic. The goal is to minimize how often they happen. When you regularly monitor equipment performance and have a plan to keep it operating efficiently it is more likely you will be able to avoid major shutdowns altogether. Having a schedule for things like routine tank blasting and maintaining the paint and coating not only improves how the equipment operates but also aids in your facility’s compliance with regulatory health and safety requirements.
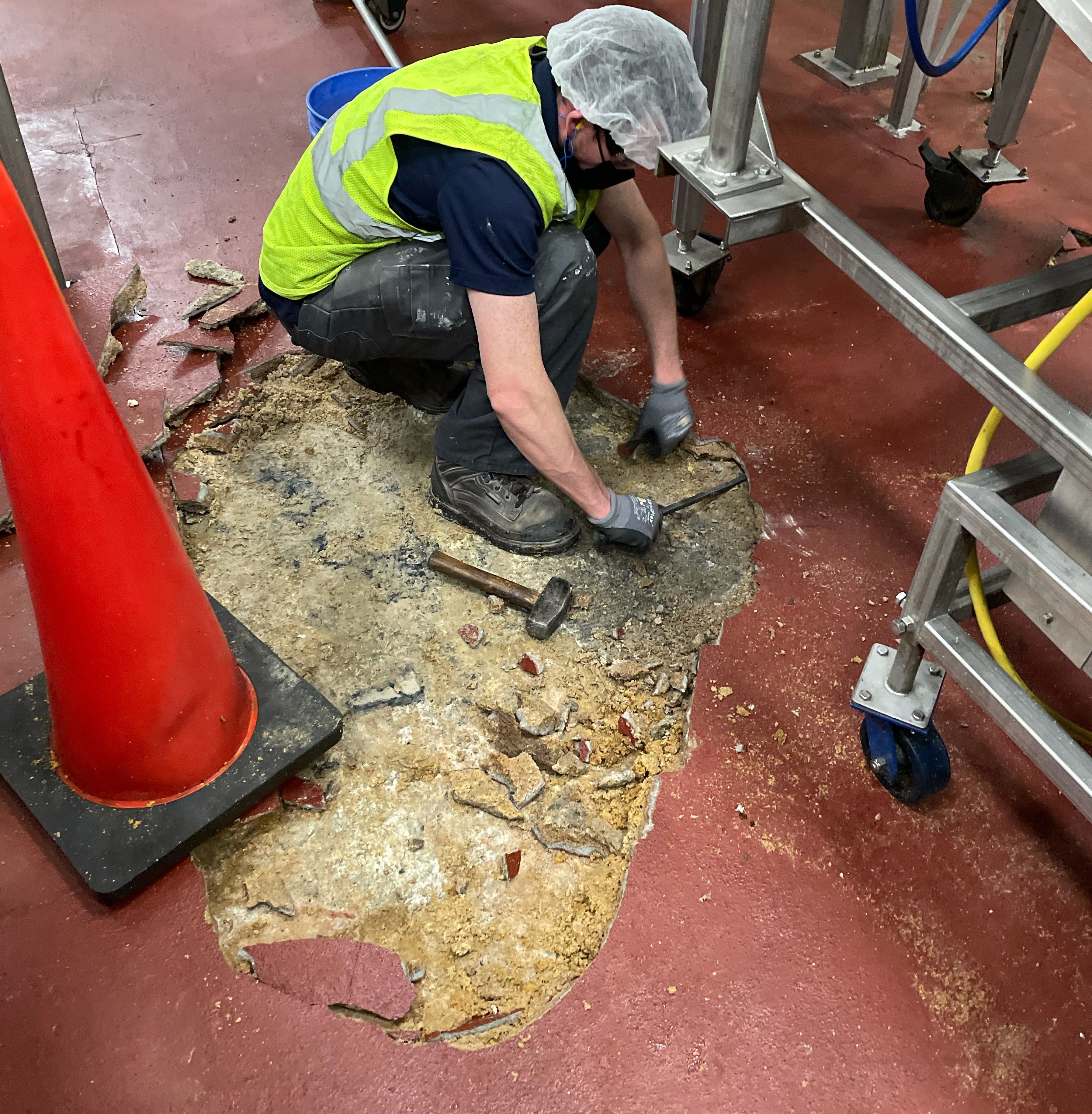
By regularly monitoring equipment performance and adhering to a well-designed maintenance plan, you increase the likelihood of avoiding major shutdowns altogether. Instead of waiting for a critical failure, a preventative maintenance approach focuses on the early detection and resolution of potential issues. This proactive mindset enables you to address minor malfunctions and make adjustments before they escalate into significant problems that disrupt production and incur substantial repair expenses.
A key aspect of preventative maintenance is the implementation of a schedule that includes essential tasks like routine tank blasting and the maintenance of paint and coating. These activities go beyond mere performance optimization. They also contribute to your facility's compliance with regulatory health and safety requirements. For instance, regular tank blasting helps remove accumulated debris, scale, or contaminants, ensuring the proper functioning of the equipment while reducing the risk of contamination. Maintaining the paint and coating safeguards against corrosion and other damage, preventing potential hazards and maintaining the integrity of your products.
In addition to improving operational efficiency and regulatory compliance, a preventative maintenance plan also offers several other advantages. It extends the lifespan of your equipment, as regular upkeep helps prevent premature wear and tear. By identifying and addressing minor issues early on, you prevent them from escalating and causing further damage that may necessitate costly replacements.
Moreover, a proactive maintenance approach enhances the reliability and consistency of your production processes. When equipment is operating efficiently, you can maintain a steady workflow, reduce unplanned downtime, and avoid costly delays or interruptions in meeting production targets. This not only boosts productivity but also helps build a positive reputation among customers by ensuring timely delivery and consistent product quality.
Furthermore, a preventative maintenance plan promotes a safe working environment for your employees. By actively addressing equipment malfunctions and hazards, you reduce the risk of accidents and injuries. Regular inspections and maintenance procedures provide an opportunity to identify potential safety concerns and rectify them promptly, fostering a culture of workplace safety and well-being.
WHY SHOULD YOU PLAN?
Preventative routine maintenance saves time and money. Being proactive instead of reactive, increases the chances of avoiding emergency repair costs on finding parts and personnel. In food and beverage manufacturing a shutdown could also mean wasted products and materials due to contamination or spoilage.
When you do need to shut down for repairs or required maintenance look to plan proactively to maximize your downtime. Check your schedule for optimal dates and times that align your schedule with other shutdowns or slowdowns in business. Blast It Clean values your profitability and will provide a flexible schedule to meet your needs. That means working overnight, weekends, around-the-clock shifts, or whatever it takes.
Overall, a comprehensive preventative maintenance plan offers numerous benefits to food manufacturing facilities. It minimizes unplanned breakdowns, enhances equipment reliability, improves regulatory compliance, ensures consistent production, extends equipment lifespan, and promotes a safe working environment. By investing in proactive maintenance practices, you create a foundation for operational excellence, cost savings, and sustained growth in your facility.
WHO CAN HELP?
None of the planning and preparation will pay off if you aren’t working with an experienced industrial contractor. When you are looking for a company that can meet your needs and optimizes time, it is crucial they understand your business. In food and beverage manufacturing that means being familiar with health and safety regulations. Working with a company, like Blast It Clean, which is conversant with the Current Good Manufacturing Practices ensures the continuity of your plan for food safety.
This knowledge and experience will also equip you with a partner. Instead of just providing a service, a company like Blast It Clean can provide options and create solutions that benefit your business. We know what tools and techniques are appropriate and efficient. For example, dry ice blasting is a great technique in the food industry because it cleans and sanitizes without leaving behind residue. It is also FDA-approved. We can also recommend specific coating solutions based on your needs and uses that may make upkeep easier so you can decrease the frequency of major industrial cleaning.
BLAST IT CLEAN CAN HELP YOU
Are you in need of assistance in setting up a comprehensive maintenance plan for your facility? Look no further than Blast It Clean. With our specialized cleaning and coating services, Blast It Clean is well-equipped to support your preventative maintenance programs. By leveraging our expertise, you can optimize the efficiency of your maintenance operations and achieve long-term cost savings.
One of the primary advantages of partnering with Blast It Clean is our ability to provide services that can be put on autopilot. Routine cleaning tasks, when performed regularly and systematically, can eliminate the need for additional expensive equipment. By implementing a proactive cleaning schedule, you can prevent the accumulation of dirt, grime, and contaminants that can lead to equipment malfunctions and reduced performance. Blast It Clean's experienced team understands the specific cleaning requirements of the food manufacturing industry and can develop customized cleaning solutions tailored to your facility's needs. From equipment cleaning to surface preparation, we utilize state-of-the-art techniques and equipment to deliver thorough and efficient industrial cleaning services.
By entrusting your cleaning needs to Blast It Clean, you can take advantage of our expertise to identify areas where routine cleaning can streamline operations and eliminate the need for costly investments. Regular maintenance cleaning not only enhances the longevity and reliability of your equipment but also contributes to a safe and hygienic working environment. By reducing the risk of contamination and product spoilage, you can maintain the highest standards of food safety and regulatory compliance.
Furthermore, Blast It Clean recognizes that every facility experiences slowdowns at certain times. Instead of letting these periods go to waste, Blast It Clean can help you maximize your downtime and keep money in your pocket. By leveraging our flexible scheduling options, including overnight, weekend, and around-the-clock shifts, we can efficiently perform maintenance tasks during these slower periods without disrupting your regular production activities. This strategic approach enables you to minimize the impact on productivity while ensuring that essential maintenance tasks are completed.
When you collaborate with Blast It Clean, you gain more than just a service provider; you gain a reliable partner who is invested in your success. Our experienced team understands the unique challenges and requirements of the food manufacturing industry, including compliance with health and safety regulations. Blast It Clean's expertise allows us to go beyond providing services to offering valuable insights and solutions that benefit your business. Whether it's recommending specific coating solutions or suggesting more efficient cleaning techniques, we are committed to finding ways to optimize your maintenance processes and contribute to your facility's overall profitability.
Give Blast It Clean a call today to discuss your specific needs and find out how we can assist you in setting up an effective preventative maintenance plan. Our team is ready to provide you with the support and expertise needed to keep your facility running smoothly and efficiently.